Getting old is a &*#*$.
I've got a bum knee that's been gradually getting worse. Over the
past several years, it particularly hurts when I sat in my Fly
Baby. Not sure why; something about the seating position, I guess.
One thing did make it worse: Because all the aircraft avionics
are built into a box in the center of the floor between my legs, there
was nowhere to move my legs after I sat down. Being locked into a
position...particularly a position that hurt to start with... was
really giving me problems.
The solution was to get rid of the damn box.
One wee problem: The box held the Transponder, the voltmeter, and
ammeter, the hobbs meeter, five combination circuit breaker/switches,
and two additional switches. They'd all have to go
somewhere....and there was limited space to which they could go.
As this picture of my panel shows, there's not a lot of spare real
estate!
Other Mods
While I was at it, I was going to fix a few things about the existing
electrical system design that I didn't care fore.
The first was the lack of a power solenoid. The master switch on
most airplanes activates a big relay. With the master switch off,
power is completely removed from the aircraft systems.
Not so with Moonraker. Power was *live* all the time; there was
no electrical or mechanical disconnect for electrical power short of
physically disconnecting the battery. Power was live to the
starter all the time.
I didn't like this...it had thrown sparks, and given me burns, a couple
of times in the past. Time to fix it.
The old avionics box had what was essentially an avionics master; I'd
put a new, smaller one in.
Access
Getting a Look-See
My airplane has a Microair
transponder which installs in a 2 1/4" instrument hole. Sadly, I
*did*
have a 2 1/4" hole available... where the Fun Meter was installed.
The problem was the depth. I couldn't measure it well through the
removable center panel without removing it, but it was darn close to
seven inches....which is the minimum mounting depth for the Microair.
I needed to get good, easy access behind the panel...not just to get
good measurements, but to have things wide open to do the wiring.
Moonraker was built almost perfectly to plans, and had a large metal
cover running over the fuel tank, from the instrument panel to the
firewall, with 3/16" bolts through the upper longerons into anchor
nuts. In the sixteen years I'd owned the airplane, I'd never take
it
off. I didn't know if the anchor nuts were frozen to the
nuts...and if
one of those anchors came loose, it'd be a devil to get at. The
screws
had been installed over 30 years ago...how likely were things to turn
easily?
However, the first concern was the landing-wire anchor terminals.
They
went through a tiny slot in the cover, which meant that the terminals
would have to be removed first. And, of course, it's the landing
wires
(and the terminals) that support the wings on the ground.
The problem was, I'd never pulled the wings on 'Raker. I didn't
have
any proper supports in the hangar to hold the wings up while the
terminals were disconnected. Pete used a broomstick cut to
length...I
didn't even have that.
Before solving THAT problem, I decided to see what the status of the
screws was. They were Phillips head, so I grabbed an assortment
of
name-brand screwdrivers. I didn't want one of soft metal that may have
rounded a bit and might strip out the heads.
Put the screwdriver in the first one on the left side, rotate it ever
so slightly to the right, first (hopefully to break up any rusting),
then start backing out. Tight, but came out normally. All
the ones on
the left side came out fine, though the ones on the green paint were a
bit clogged with paint.
To the right side. Most came out OK, but the screwdriver head
popped
out of one of those in the green. I tried it with a slightly
smaller
screwdriver, same deal. I dug out all the paint I could from the
screwdriver slot with a short piece of safety wire. I put in the
big
screwdriver, leaned hard into it, then eeevvvverrrr so slowly started
turning it to the left. It worked; the screw came out of the
fuselage.
I tightened them all back up (might be able to fly tomorrow), and
looked at the slot where the terminal stuck through. Easiest
thing to
do, once the cover was off, was to just cut out a full-width slot to
the bottom of the panel (a couple of inches). I may try to come
up
with a cover for the area that can be removable.
Supporting the Wingtips
Now to come up with some sort of wingtip support to hold the wings up
with the terminals loose. I've got a little folding, adjustable
roller
support for my woodworking, but I wanted an interface that would be
kinder to the fabric undersurface of the wing. I wanted something I
could just leave at the hangar, and not have to fetch it if I was
cutting plywood at home.
A certain national tool-supply chain had just opened a new branch just
five minutes from my house, so I figured I'd wander through there and
see if they'd have cheap versions of my roller support, and maybe a
battery cable crimper for doing the #6 cables later. I won't name
the
outfit...let's just call it "Bayside Shipping," or BS for short.
I grabbed my "Free flashlight with any purchase" coupon and drove
over. Wasn't too busy; kind of a surprise for a grand opening
weekend. I indeed found a roller stand for just $15. It had
the
roller head held on by bolts...perfect, I could just replace it with a
padded holder.
Got it home and started assembling. Funny, just could get the
first
bolt to thread onto the nut. Found out why when I took a closer
look....
Go back to BS and demand a replacement? Uggh, hate to do that for
a
lousy little screw. I checked the parts list, and I could replace
the
faulty bolt with some of my stock.
So, back into the assembly. Both feet went on, then I started
threading the clamp handle. The clamp holds the sliding end in
place
by screwing into a threaded section on the housing and pushing against
the sliding portion inside. I tightened and tightened and
tightened,
but it never clamped up. The threaded bit was stripped.
NOW take it back to BS? Well, it still had some usable parts, and
COULD be made to work. So I drilled out the clamp hole on the
housing
to go all the way across, marked 1" intervals on the sliding bit
(box-section tubing), then put it in, aligned the mark to the first
hole, and drilled out both sides.
My bits are pretty old and pretty dull, so I anticipated a long slog
drilling holes from either side in that quality BS steel. It did
not
take long.
I installed the standard roller on top of the Bayside Shipping
adjustable stand, but with only one bolt to it'd tilt. It slipped
nicely under the wing; I adjusted it close with the holes I'd drilled
yesterday, then stuck a big hunk of foam between it and the bottom of
the left wing. I slipped a sawhorse under the trailing edge, just
as a
backup.
The holding screws for the forward turtledeck had already been loosened
yesterday, and almost all came free without a hitch. The anchor
plate
had come loose on one, but since it was the one in the cockpit, it was
easy to grab and secure.
All the bolts came out bright orange...30 years of contact with the
wood. Structurally, they appear fine. Might replace with
stainless,
or might buff 'em up a bit.
With the cover free, it was time to slack off the wing bracing and
slide the landing-wire terminals through the slots in the cover.
I put a bolt through the hole drilled in the right-wing terminal strap
(to hold that wing in place as the master turnbuckle slackened) then
started cranking on the Master Turnbuckle, using an allen wrench as a
lever through the center holes.
In the past, I've always had some confusion as to which way to turn
it... then I realized: "Stick forward for grounding, Stick Up to
fly."
So I pushed the top of the allen wrench toward the instrument
panel,
and things loosened nicely. As things got loose, I'd wander out
to the
left wingtip, lift the wing a bit, and kick the stand a bit further
under it.
Finally the left clevis pin was free. I slipped the terminal out
of
the slot, lifted the cover free, and re-inserted the terminal and
hooked it back up to the turnbuckle. I had to re-tighten the
turnbuckle a bit to get the left-side hole far enough through the
terminal mount to put a bolt through the hole, but the right side bolt
came out at the same time and I just repeated the process. Very
simple.
With that, the cover was mostly free...the only thing holding it down
was the gas cap and the rubber gasket that goes at the base of the
filler. Take 'em off, and the whole cover lifted away nicely,
exposing
the entire forward fuselage top.
One slight immediate disappointment: I had hoped the gas tank
didn't
go all the way to the firewall so I could get easy access to the rudder
pedals from above. No such luck.
Other than that, though... fantastic. I'm a big believer in
maintenance access, and taking this panel off opened exactly the area I
wanted easy access to.
Fitting the Parts
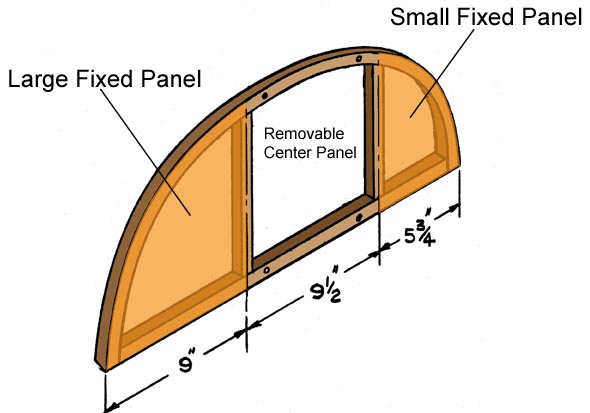
At the start of this web
page, there's a "before" picture of my panel. The picture is
actually a bit deceptive. There's a 3/4" wood
frame behind the panel, and two vertical supports
on either side of the center panel. What looks like usable real
estate
really isn't. Remember that most parts, like the gauges and the
radio
mount, actually take up more space behind the panel that they do in
front...and all that framing gets in the way. Look at the picture
above and see how far the compass is from the top of the panel. I
actually had to slice away a teeny bit of the frame to clear the
compass when I built that panel!
So, what to do?
Making the panel larger wasn't an option. If I was going to cram
more
stuff into the available space, I needed to combine some
functions.
Like, get rid of some of the current gauges and install gauges that
combine multiple functions.
The trouble is, they don't do that much, with round-type gauges.
I
could get a combined oil pressure/oil temp gauge, but my current units
were 2 1/2" gauges and the replacements are usually 3" units.
Going High Tech - At First

But there *are* some products that combine multiple
gauges into single boxes: EFIS, or Electronic Flight
Instrumentation Systems. The Dynon EFIS-D6, for instance, has
airspeed, altimeter, rate of climb, artificial horizon, compass,
slip-skid, voltmeter, and, no doubt, a thing which tells time.
All in a little tiny box pulling a little tiny amount of power.
Ludicrous thought, huh? A digital panel in a Fly Baby. Two
thousand bucks of electronics in my little termite haven. Har,
har.
But....but....
Damn, it WOULD free up a lot of panel space...getting rid of three of
my existing gauges, two of which were full-sized 3 1/8" units. I
did have a concern about sunlight readability...it'll be out in the
open, would the sun wash out the display?
But two thousand bucks.
I mentioned it to my wife, and she said, "You've been working a lot of
overtime lately...why not spend it that?"
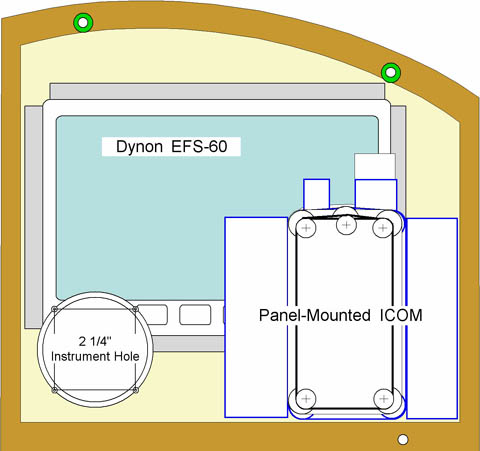
Whoa. Five minutes later, I sent an email to
Dynon: "I've got a Fly Baby that I thinking of installing an EFIS
in...how readable it it, in an open cockpit?"
The phone rang five minutes later. "It's somebody
from...Dynon...?"
said the wife.
Turns out the person handling the emails is the daughter of one of my
EAA buddies, and I'd met her a number of times at Chapter functions
(and
also spoke at her high school). She saw my name, said, "There
CAN'T be
two of them!" and gave me a call.
We talked for a bit. Yes, the Dynon is sunlight readable... folks
buying the new Wacos often install them.
OK, time to get serious.
Sadly, (sniff) it didn't work out. I just couldn't get the thing
to fit. Since there was restricted space behind the panel, I was
limited to their rectangular units. I wanted to mount the Dynon,
the existing comm radio, and the transponder (a 2 1/4" Microair unit)
in the removable center panel area, and there was just no way.
The unit that mounted in the standard instrument hole would have
worked, but the fuel tank is too close to the instrument panel.
The unit itself requires about seven inches, but I had only about six
and three quarters (and would need space for connectors as well).
The only option was a COMPLETE re-plan of the panel...getting rid of
the three separate sections and building the panel as one combined
piece. It would have worked, but it would have required major
rework. I really wasn't ready for that.
So...sadly, I gave it up.
Disappointment, and a Potential Alternate
Unfortunately, it was quickly apparent that there was NOT a whole lot
of room for more switches and the transponder.
I took a tape measure to the right side, where the "Fun Meter" is at,
to measure how much clearance I had from the fuel tank. It was a
total of about 6 3/4", with 6" to the edge of the instrument panel
frame, and a ~3/4" frame to the panel.
*Might* be doable... but there's a big support for the gas tank down
low, and it looks like it'd interfere.
It could be installed poking out like the one in the Victoria Squadron.
But the situation on the other side of the panel, where I'd
hoped to install the switches, was bad, too.
Just looking at the left side of my panel...
...it looks like those gauges can be crammed together quite a bit more.
But the other side of the panel tells a different story:
The oil temp and pressure gauges have big support structures behind,
and the mag switch is big as well. There's room around the Tach,
but probably not enough to install a nice-looking row of
switches. The frame for the panel is about 3/4" wide, robbing
quite a bit of real estate.
"But there's a big open stretch at the bottom"? Yes, but on the
PILOT side, that's where the landing wire terminals and block.
So it initially looked like this approach was a bust. There
wasn't enough room to install the transponder, nor was there enough
room for all the switches and circuit breakers. The only thought
at this point was to build a new Avionics box, miniaturized when
compared to the existing one. The trouble was, that approach
didn't free up the legroom as I wished.
However, there was one big thing in its favor: Over the years, I
had installed connectors for where the various components attached to
things in the Avionics box. I should be able to build the box
separately, and just plug it in. A lot easier than reworking the
panel.
The Mapleair Transponder
But you know... I really didn't want a box on the floor. I wanted
the space unobstructed.
The main kicker was the transponder. Time to look at whether I
could make it fit. Since I hated fumbling that $2,000 Microair
around as a template, I decided to build a wooden replica: The
"Mapleair".
I grabbed an old bit of 2x4 and cut it out to the dimensions of the
box. I added a raised face (to fit inside the 2 1/4 instrument
hole), printed the instrument face onto a bit of label stock, and
nailed in a piece of dowel nailed down to simulate the adjustment knob.
Went to the airport, and was able to maneuver it into position:
Unfortunately the back end just BARELY fit inside a wood support for
the fuel tank:
The Mapleair does not include the coax fitting or the ribbon-connector
socket on the back. That support hits RIGHT where the coax should
go, and at the top, the DB-25 connector is just ~3/4" from the
tank. This is so tight the Mapleair isn't even screwed in place
for the photo.
Moving it up isn't really an option. The existing 2.25"
instrument hole that I used (which mounted the "Fun Meter" before) just
barely has clearance for the transponder within the instrument panel
frame. Plus, since the instrument panel leans back slightly,
moving it up will actually reduce the clearance at the ribbon
connector. Here's a shot showing the "Fun Gauge"...its exterior
dimensions are about the same as the transponder, and you'll note
there's not much room to move up.
So: It looks like "Conventional" mounting, here isn't going to
work.
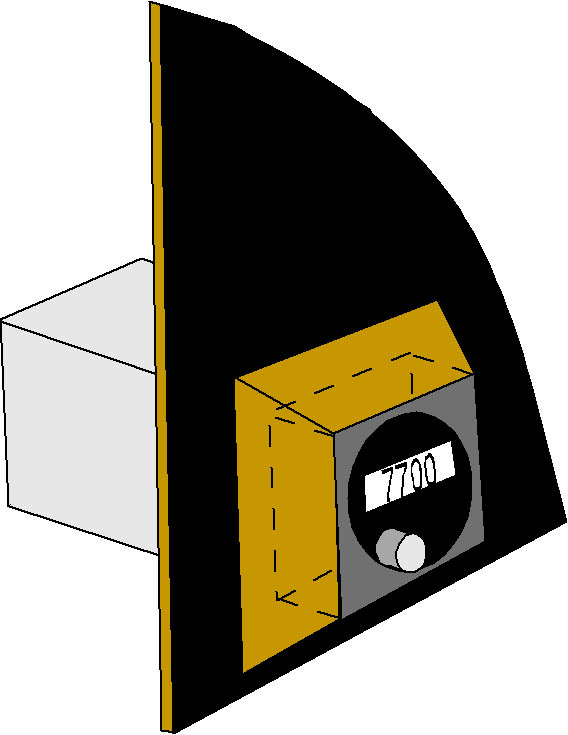
The Victoria Squadron made a
wider hole and let the transponder protrude into the cockpit a
bit. A friend at work suggested I could even make a sort of
"bezel" out of millwork and make it look less like it's just sticking
out. Making a new panel for this side would let me move the
transponder down slightly, and maybe free up some room for some
switches above it.
Commitment
Everything I'd done so far has been cosmetic only; I could take a
half-hour and button things back up and go fly. Finally, it was
time for commitment, it was time to start cutting out wood and
disconnecting the existing electrical system.
First step was to remove the center-section of the panel...pretty easy,
and that's exactly what it was designed to do. After that, I
needed to remove the right-side triangular panel that held the "Fun
Gauge" and would hopefully hold the transponder. It was glued
with a few nails, per Pete's plans. Originally, I was just
cutting out the inside to lay the new panel atop the old, but one of
the pieces I stripped away took some of the panel glued atop the frame
as well. So I got the razor saw and some chisels out and went to
work.
One of the things that was more-and-more apparent is how great the
access is with the turtle deck cover off. I noticed today that it
looks directly down at the top of the avionics box. I was able to
uninstall the transponder with a HECK of a lot less effort. I
realized, too, that I could not only see the rudder pedal cable
connections clearly from above, I could even reach them by using the
gap between the fuel tank and panel.
There was even the former headset jacks that I could access well enough
to use, back when I converted the ICOM. They were mounted on an
angle bracket BEHIND the panel. With solid access, I was able to
remove them.
I noticed, too, some drawbacks for my "blind" work behind the panel,
before. The end of a piece of safety wire was resting against the
fuel tank and scratching it. Minor, but it shouldn't be like
that. Good opportunity to fix it.
I did a test-fit with the Mapleair and it looks like my mounting
concept should work. There was enough slack on the Transponder
ribbon cable (the data cable) to reach across the cockpit to the new
transponder home. However, once I looked at the end connector on
the data cable, it was obviously too long. The fuel tank would
get in the way of connection But it's a standard DB25 connector,
and I found a low-profile right-angle adaptor for $10.
The Perils of Education
I've always been a voracious reader. As a kid, I found a stock of
books my mother had received in the '40s in a book club. One
became my favorite... Bill Mauldin's "Up Front," containing copies of
his WWII cartoons and a lot of information about his life in the Army
during the war.
A while after I discovered the book, it disappeared... Mauldin's
characters said "Hell" and "Damn" in his cartoons, and Mom didn't think
an eight-year old should be reading that sort of thing.
But the cartoons stuck; it got to be that they often seemed to relate
to my own experience in life.
Had one while shopping for switches. Nearly 70 years ago, Mauldin
drew a cartoon of two GIs in a foxhole. Shells are exploding
overhead, bullets are whizzing past. One GI is crouching low, but
the other one is crawling over the edge, leaving the safety of the
foxhole.
He's saying, "Wish ta hell I wuzn't housebroke...."
In my case, sometimes, I wish to hell I wasn't an engineer.
As I mentioned in an earlier posting, I was scanning the racks of the
local auto stores for DC switches for the Fly Baby electrical rebuild.
I needed something small, small enough to put three in a row in a
fairly limited area above the new Transponder location. I also
wanted something...stylish. Something more than just a couple of
silver toggle switches.
Found 'em at the car parts store Three tiny rocker switches, just
a half-inch wide, rated at 20 amps at 12 VDC (I think I need 20A for
the generator field circuit). Three different colors. They
even light up. $4 each.
Got 'em home, but then the engineering brain started to work.
They're rated at 20 Amps...but will they really HANDLE 20 amps? I
took one out of the bubble pack, and wasn't too impressed with the
quality. The switch body is single-piece, and the rocker looks
like it was pressed in at the top. The rocker itself pivots on
two little protrusions from the plastic...took no imagination at all to
picture one of the little "ears" breaking and the switch coming apart
on the panel. And then I have to remove the panel again, pull the
switch out, find a replacement, etc.
I just got really reluctant to install three of those cheap things in
my panel.
Sigh. The problem is, there REALLY isn't a lot of room to mount
switches above the spot the transponder is to go. The panel
itself is big enough, but the instrument panel frame robs quite a bit
of internal area.
I found a Cessna split master/generator rocker switch in the Aircraft
Spruce catalog. I figured 10,000+ Cessnas couldn't be wrong, so I
went ahead and ordered it. No dimensions given...so I didn't know
if it would actually fit in the available space on the little
panel. Just betting on the come, as they say.
Building the New Panel
The good news is, it looked like the Transponder would fit. I built a
one-inch high "picture frame" around the hole in the new triangular
panel from 1/2" wide wood, and glued it to a piece of 1/8"
plywood. I tilted the tablesaw blade ~15 degrees or so and
tapered the frame down a bit (e.g., 1/2" wide at the bottom, ~1/4" wide
at the top" and rounded the front edge..
The transponder itself fit, but the antenna connector was almost
directly adjacent to the fuel-tank brace. I noticed the brace was
held to the longeron by two wood screws. I took a chance that it
wasn't glued as well, and it paid off: 30 seconds to remove the
brace, take it to the bandsaw, chop off ~1/2 the length of the leg,
reinstall...and now the antenna cable will connect.
I didn't like how tight the antenna connector was, so I'm using a
90-degree BNC connector.
Positioning the transponder slightly lower on the triangular panel left
juuust enough room for the Cessna split master switch. Mounting
the switch was a bit weird; it has a thin spring-steel frame that snaps
in the front of the opening, and the switch itself snaps onto the frame
from behind. This picture is of the back side of the panel...the
dark line is the limits of the opening. The white label shows the
outline of the Klixon circuit breaker.
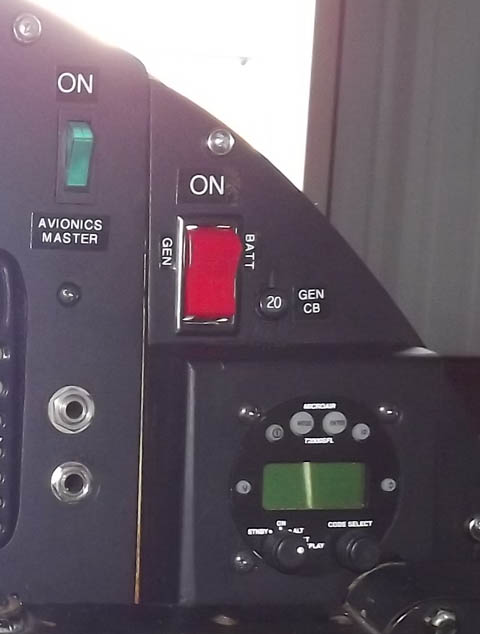
The label above, by the
way, is how I established the guide for all of the cutting on the
panels. In this case, the square just shows the extent of the
circuit breaker, while the little "plus" indicates the position to
drill the mounting hole. I used similar labels for the Master
Switch and for the Avionics Master, but in these cases, the box
indicated the material to be removed. I printed the label using a
Brother desktop mailing label printer, positioned it on the panel,
drilled a couple of holes, and then used a scroll saw to cut out the
rectangle. I always made the rectangle slightly small, and
enlarged the hole by hand to keep from cutting too far. Worked
pretty good.
Labeling was done using a Brother P-Touch label machine.
With the brand-new paint on the brand-new side panel, the rest of the
instrument panel looked scruffy in comparison. I had to remove
the center panel to install the avionics master switch anyway, so I
removed all the gauges and repainted the panel.
Here's a shot of the finished panel, showing the split master, the
circuit breaker, and the avionics master rocker switch on the center
panel section. The avionics master switch light up, when on.
The left-side panel was VERY scruffy, and I didn't have a convenient
way to remove it. I left all the gauges connected, but unmounted
them, either pushing them behind the panel or pulling them in front,
depending on how they mounted. I masked off the holes for the
ones that went behind the panel, and wrapped the Oil Pressure and
Temperature gauges with masking tape since they pulled in front of the
panel.
I then masked off the panel area and hit it with the same rattle-can
black
paint the rest of the panel received. The trouble is, I didn't
mask off the oil pressure gauge well enough. You can see a tad of
overspray on its face.
I needed a voltmeter, and the one left over was a big 2 1/2" unit that
I wouldn't have room for. Instead, I found a tiny digital
voltmeter
from
Marvel
Meters . It
has a big screen on the "pilot" side, but it mounts through a single
3/16" hollow stud, with the wires coming
through it. It cost just $40. I installed it into one of
the holes
that mount the handheld radio to the panel. You can see it in the
photo below.
Planning Problems
I got into this project on the spur of the moment...I was having leg
problems with the constricted seating position, and wanted to get rid
of the floor-mounted avionics box so I could move my legs a bit.
My "mental design mode" was that the changes would consist of the least
amount of work necessary to transfer functions from the avionics box to
stuff mounted on the panel.
But I really hadn't thought things far enough out. The avionics
box has a switch that applies 12V to the regulator. Looking at
the Bingelis diagram, HE didn't show a switch like this... so I didn't
plan on one.
What I did miss is that he DOES show a fuse on that line...and the
switches on my avionics box were actually combination switch/circuit
breakers. My mental attitude was that I'd re-use switch/breakers
for all functions. But when I took out the Avionics box, I
discovered those switch/breakers are HUGE. No way could I fit
them anywhere on that triangular panel.
I needed a fuse for that Generator line. Fortunately, there was
room for a cylindrical-style Klixon breaker in the remaining
area on the triangular panel with the master switch and transponder.
But, of course, if I'm NOT using the switch/circuit breakers... that
means I have to incorporate both switches and circuit breakers or fuses
into all the electronics. And there really isn't enough room for
everything.
I have fuses for the radio and transponder anyway, hence the single
avionics master. That still left me with adding fuses
and switches for the position lights and strobe. I don't really
want to remove and rework the left side of the panel; the little
triangular panel was tough enough to cut away. But I think I can
fit the switches for the position lights/strobe on it, anyway. I
might be able to install the fuses on the wooden cross-beam underneath
the fuel tank. No real rush on these, since I'm flying as a Sport
Pilot and can't fly at night, anyway (and haven't flown at night for 15
years).
My poor planning had mentally said, "Re-use the wires that go from the
regulator to the avionics box." But when I got the avionics box
out, I realized the wires were probably too short to go where I needed
them...and were ordinary wire, not durable aircraft wire. It
appeared in great shape, for 30-year-old bell wire. But I might
as well re-wire it...and, oh, I need to order some 12-gauge shielded
wire, now.
So...it turned into a complete re-wiring job. There's a ton more
stuff I needed. First step would be to actually make a SCHEMATIC
of the re-worked electrical system so I can understand what I'm
actually going to need.....
Planning may have begun late, but I can at least say that planning
finally began.... The panel was done, it was time to wire things up.
The Electrical System
A Schematic, Hurrah!
OK, this is what I came up with. Basic design is in Tony
Bingelis' books....
Solenoid
As I mentioned way back in the beginning, I wanted to add a master
solenoid to the aircraft.
The plane had an existing insulated stud pass-through for the 12 V
positive battery, so I figured I'd hook the battery to the solenoid and
pass the power to the firewall side via the stud.
I needed a short piece of heavy wire (I used 6 gauge) to go from the
solenoid to the pass-through. I basically needed a very short
battery cable with lugs on the ends rotated 90 degrees to each other.
But how to build? It obviously needed a dedicated tool to swage
the two fittings onto the end of that very heavy wire.
A friend came by the hangar while I was puzzling on this problem.
I asked if had a battery-terminal swage. He did...but for #2
cable; too big for #6.
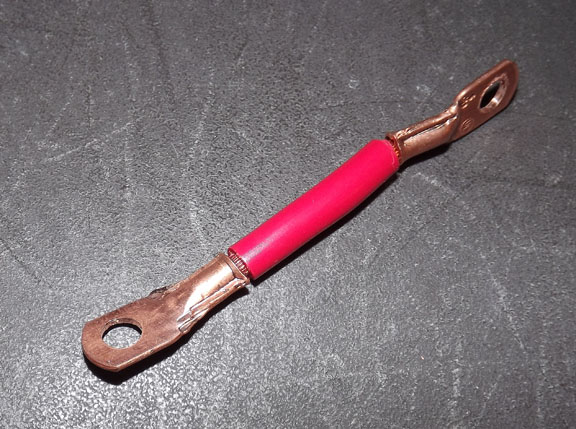
Then he asked me: "Do you have a swage for
Nicopress fittings?"
I blinked, a little aback by the apparent change in subject. "Yeah...?"
"Use that."
The idea really appealed to me. When I got home, I took a bit of
cable and one of the terminals, put 'em in the 1/8" side of the swage,
and cranked away. Came out looking absolutely beautiful.
Stuck a screwdriver through the hole in the terminal, tugged with all
my might. Still solid. Put the terminal at the other end,
rotated 90 degrees, and take it to the airport.
I looped the lug for the cable around the pass-through stud, put the
other end to the Solenoid, then swung the assembly to a level
installation attitude and drilled the holes for the solenoid.
Whoops, a bit close to the center support (on the cockpit side). Still
will work, though.
Unfortunately, it was too close for that short piece of #6 cable...
over the ~4" length, it hardly would flex at all.
The irritating thing was that I didn't want to re-drill the mounting
holes for the solenoid. Which meant that I had to make another
piece of cable that was almost exactly the right size.
While I was at it, I fabricated the protection diode assembly.
Master solenoids work by grounding the control terminal; the coil
inside gets its +12V power from the battery cable. The problem
comes with the nature of coils... most folks are familiar with
capacitors which attempt to hold a given charge voltage at the
contacts. Coils are exactly the opposite; once operating, they
want to keep a *current* going. Which means that when the power
at the coil goes off, it still tries to push current. This can
damage electronics on the main bus.
A diode allows current to pass in one direction. On the solenoid,
it's set up to be "reverse biased"... so that it's set up between the
control terminal and the battery terminal so that current doesn't
normally flow. I covered the diode with red and black shrink
wrap. You can see it in this completed-installation photo, as
well as the way the solenoid runs slightly atop the triangular brace.
The completely-covered terminal on the left is the +12V from the
battery. I've got the same kind of rubber boot on the output
side, but it does gap a bit with the other terminals coming out.
Wiring
Wiring was pretty-well straightforward. I had bought aircraft
wire in various colors from Aircraft Spruce, and had a gen-u-wine
aircraft crimper to apply the terminals.
The 30-year-old commercial wire used originally in Moonraker seemed to
still be in good shape, but I felt better going with wiring that was
designed for the application. Curiously, the aircraft wire was skinnier
than the same-gauge commercial wire...thinner insulation, but a lot
harder.
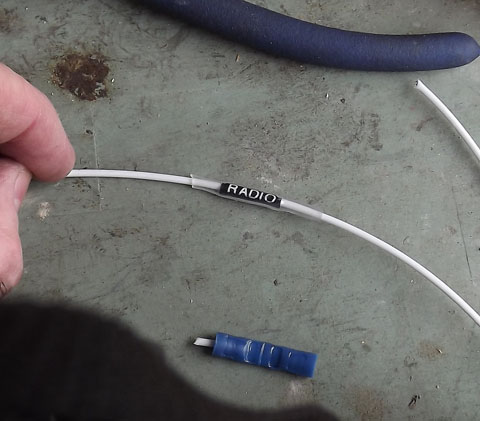
Just about everything behind the panel used standard
slide-on
terminals, so the wiring itself was pretty straight forward.
Generally, the connection was a slide-on terminal on one end, and a
ring connector to fit the positive/negative bus points on the other.
One thing I did was to use a P-touch labeler to generate
labels for the individual wire, holding them in place using transparent
shrink wrap.
I added Molex connectors for the radio and transponder, and used the
P-Touch to label both the connectors and the antenna leads. I
used the right-angle adaptor for the DB-25 connector on the
transponder, and the existing cable hooked right up.
One problem to solve was the stringing of the wiring. The easiest
route was along the top of the right-side top longeron. Three of
the wires wires had to penetrate the firewall to go to the Regulator
and Generator. They had previously gone through a penetration low
in the center of the firewall; this was very convenient with the
Avionics Box mounted on the floor of the aircraft. However, I
hated to make all the turns and everything in the cockpit area, where
access around the fuel tank was difficult. I contemplated making
a
new hole in the firewall near the top, to let the regulator and
generator wires exit directly into the engine compartment. Those
are the bright red lines in the diagram below.
However, I opted to run them out the existing hole. I had to run
two wires down the back of the firewall anyway (because the solenoid
was mounted down low back there). My planned routing was forward to the
back of the firewall, down to the lower right corner, then across to
the lower center where the pass-through and the solenoid were.
However, this caused the wire bundle to
be directly in front of the right brake pedal, and, with the brake
fully depressed, there was a danger that the pedal would pinch the wire
bundle. Instead, I led it aft, behind the pedal, then curved it
back forward to the solenoid and pass-through. That's the dark
blue line on the diagram.
The photo bellow shows the routing of the wiring on the top of the
longeron. Self-adhesive tie-wrap mounts are installed on the
fuel tank straps to hold the bundle. Aft of the fuel tank, you
can see the replacement fuel-tank brace.
I'd been waffling about how to design in a ground terminal and a 12V
terminal to give common connection points for the rest of the
electronics. I realized that the fuel tank brace being removable
was the key... I replaced it with a "T" shaped one (that follows the
longeron further aft) made of 1/2" plywood and put two studs in it
where the plus and minus
ring connectors for the radios, voltmeter, lights, etc. can
connect. These are two #8 bolts installed inverted-vertically in
it for positive
and negative bus points. Lowes' Aerospace had little plastic trim
caps
for the
head-end of bolts, and I used these to ensure the bolt heads were
insulated.
(By the way, my philosophy is to insulate BOTH positive and negative.
While many big pieces of metal in the airplane are grounded as a matter
of course, I insulated the negative power points).
You can see where the wiring harness dives down along the front side of
the fuel tank. There's a cable clamp on the inside of the extreme
forward fuselage, held in place by one of the big screws that hold the
forward flashing (you can just see the top of one of these screws on
the bottom right of the picture above). There's another cable
clamp down low, and another on the support beam for the brake
pedal. You can see how the bundle travels down, then aft behind
the brake pedal. This photo is of the system "in work," so the
far end of the cabling is still loose. When I finished up, I took
out the slack and tie-wrapped the bundle to the center support.
(If you think the brake line looks
wet...well, yes, it is. The brake line started leaking at the
fitting from the point I removed the bottom inspection panel, weeks
earlier. I had to replace the brake line before the first test
flight.)
Coax Cable
I needed to build a new coax cable for the transponder, since the old
one was too short. This turned out to be a bigger headache than I
suspected. In the past, I'd bought pre-made RG-58 coax cables
from the local electronics store...not available any more.
So, build my own. In the past, I'd done everything strictly
manually... I manually stripped the coax, soldered the tip onto the
center conductor, and assembled the connector.
This time around, I decided to buy the crimp-type tool. The
electronics store had them ($35), as well as stranded-center-conductor
RG-58 cable and BNC connectors. However, it turned out that the
connectors were for cables with *solid* center conductors. I
couldn't seem to find the stranded-type connectors.
I did find some solid-conductor RG-58. But when I did a test
strip, I was a bit dismayed...the braiding was pretty limited, and the
cable itself just seemed flimsy. Stranded cable is preferred when
bends must be made, and is generally more durable.
An online source sold stranded-type crimp-on BNC connectors. I
bought a couple of dozen, as the per-unit price was so cheap.
Instead of manually stripping the cable, I found a coax stripper at
Radio Shack that removes the outer and inner insulation in the "step"
mode required for coax. This eventually
worked great, but it did take a lot of adjustment to get the proper
spacing and depth of the stripper blades. Price was about $20.
With those combination of tools, adding the connectors to the coax was
a breeze. It's one of those cases where a little money spent on
tools goes a looong way.
Fuses
Since I was eliminating the switch/circuit breakers, I needed fuses
for the radio and transponder. The manufacturers usually
recommend the plastic in-line fuse holders. But I hate these with
a passion... over time, they get brittle, and the "ears" on the hold
break off. The spring then flings the fuse holder apart.
Not only does the unit quit working, but you end up with a live wire
loose behind the panel.
Instead, I've gotten to like the fuse-holder they sell for the ATO-type
automotive blade-type fuses. The only spring action is just
pinching the blades of the fuses, and it's well covered up by a
rubberized skin.
I could have just let them dangle in space like a normal inline
fuse. Instead, I laid down a strip of Velcro on the forward
part of the STA 3 bulkhead, right above where my knees go, and added
the matching Velcro to the fuse holders.
I have to reach for them
blind, but there's enough excess wire that I can pluck them off the
Velcro and
pull them low enough to access the fuses. I don't anticipate I'll
ever have to replace one in flight...after all, the same fuses were in
the avionics box for the past ten years (even more out of reach) and I
never had to fiddle with them. The fuse holders are light, and
the Velcro
should
hold (I've got a LOT of Velcro experience crashing my RC planes).
Even if they do come loose, they just hang down a little bit.
Smoke Test
On an project, you eventually have to come the point where you try to
let the "magic smoke" out of the electrical system. Wiring was
done, panel stuff was all connected. Time to reconnect the
battery and try it out. I connected the
positive terminal, but when I lifted the negative terminal into place,
I heard a
big CLUNK up forward. The solenoid was being activated.
Was the new Master switch on? Damn, it wasn't. Turned out
it had been installed upside down. I had taken care (I thought!) about
the switch orientation, but still hadn't got it right. I
disconnected the
wires (bless those slide-on terminals), flipped the holding clip free
with a screwdriver, verified the connectivity, then reinstalled and
hooked the
wires up again.
The ironic thing is how much this threw me off. It's a Cessna
split master switch, with one side controlling the solenoid and the
other connecting the generator to the regulator. When I tested
the
switch with my meter, I became convinced that the two halves of the
switch
were operating in REVERSE to each other...flip the solenoid side up to
turn on power, but flip the other side DOWN to activate the generator.
Eventually, I convinced myself that it didn't really work that
way. I installed the switch reversed from what it had been, and
re-connected the terminals. Hook the battery back up, no
clunk. Hit the
Master switch...and CLUNK, and the voltmeter goes active.
By the way, you can see the piece of 1/2" plywood I used to close off
the hole in the floorboards where the old avionics box used to
sit. You can see the block of wood upright on the plywood.
This was an attempt to give me a solid point to brace my heel against
when getting out of the airplane. Sadly, it was positioned too
far aft to be of use.
I checked the Molex connectors for the radio and transponder for proper
polarity, then shut off the power, plugged them into their respective
units, and powered up again. Flip on the master and the avionics
power, and both units powered up normally.
Final Stuff
Had a few final things to take care off. I applied more adhesive
tie-wrap holders to help route the comm radio coax up the side of the
fuselage. You may argue that they aren't durable, but it took a
lot of force to remove the ones that had been there before.
I checked out the way the wiring harnesses lay, and tightened them up
with tie-wraps. I'm using bright green ones; if I find a broken
one, I'll know is was part of the most-recent work.
Sit under the forward cockpit with a flashlight, looking up at the new
wiring. Secure? Out of the way of the rudder pedals?
Looks like it.
While I had everything apart, I replaced the battery. The Odyssey
dry cell battery was about eight years old, and still cranked the
engine adequately. But I figured as long as everything was apart,
I might as well do the battery. I picked one up at the local
Batteries Plus store. The price was higher than mail-order, but I
figured the shipping costs would have been pretty high.
One thing I am deferring is the re-connection of
the nav lights and strobe. They're not required for Day VFR,
which, since
I fly as a Sport Pilot, I'm limited to, anyway. I'm still
considering
the right switch locations...there's space on the left side of the
panel, but I think I can mount them low on a cockpit diagonal and save
a bit
of effort. I've actually included a spare terminal at the
solenoid
for the light bus.
Final step was to re-install the forward turtledeck cover. I used
a pair of tin snips and cut out the short piece of metal between the
slot for the landing wire terminal and the edge of the metal.
This let me slide the cover on without disconnecting the landing wires.
Test Flight
Preflight was good, the area under the new brake line was dry as a
bone. One pleasant change: Without the avionics box in the
center of the floor, it was easy to reach the fuel valve to turn it on.
I had two major worries about the electrical rework. First, the
battery cables were 4 gauge, and I'd used a short bit of 6 gauge wire
from the solenoid to the battery pass through. Intellectually,
that little 3" piece shouldn't affect anything. But if the
starter couldn't pull enough current through it, it would be a major
impact...I'd have to get someone else to put fittings on larger cable,
and I'd had to make four examples to fit that very short run.
The second stemmed from my previous generator problems. After the
last time I'd disconnected the generator, it didn't work and I had to
"flash" it. I hadn't done it this time, and worried that maybe
the generator wouldn't work.
The first issue was settled before even taking the plane out of the
hangar. With the switch off and the chocks in, I turned on the
master switch and did a quick momentary pull of the starter. Prop
seemed to turn just fine. Master switch off.
Roll the plane in front of the hangar, turn it to face towards the
taxiway. Helmet, gloves, scarf, and mount up. Sure was easy
sliding down without that box in the way.
Strap down, plug in. Master switch on, hear the clunk from the
solenoid up front. Digital voltmeter reads 12.6V (Dry cell
battery). Mags on, two shots of prime, "Clear!" and pull the
handle.
The prop turned DARNED fast. Brand new battery, and that short
piece of #6 didn't seem to affect things at all.
Darn, voltmeter didn't change. That's how it acted the last time,
when I needed to flash the generator...after flashing the battery
voltage actually dropped at low RPMs. Wasn't doing it today.
Started taxing toward the runup area. Saw a buddy working on his
plane, so pulled over and shut down to show him the new
panel. New battery started it just fine, again five minutes
later.
Warm up, run up, ready to go. Hit the runway, and pour the power
on.
As the engine accelerated, the digital voltmeter started slowly
climbing. The generator was working!
Up to 1500 feet. The voltage gradually rose to ~14 as the
generator finished recharging the battery after the two starts.
The major reason I'd undertaken the rebuild was to get rid of the box
on the floor between my legs and let my knee move around a bit to
relieve the pain. As I flew along, I was able to move it left and
right over the entire area...I was even able to pin the stick between
my knees.
It was a short flight, but all told, I sat in the cockpit for about a
half hour and felt no discomfort at all (before, I had bad pain after
just ten minutes).
It's possible, too, that the work on the airplane was good
therapy. I did a lot of getting up and down, and that may have
loosened the knee a bit.
Whatever. It wasn't hurting, and that was the main thing.
And I'm flying again. Total downtime was two months and three
days, but most of the weekends were rainy.